Why MBR technology is best for the built environment

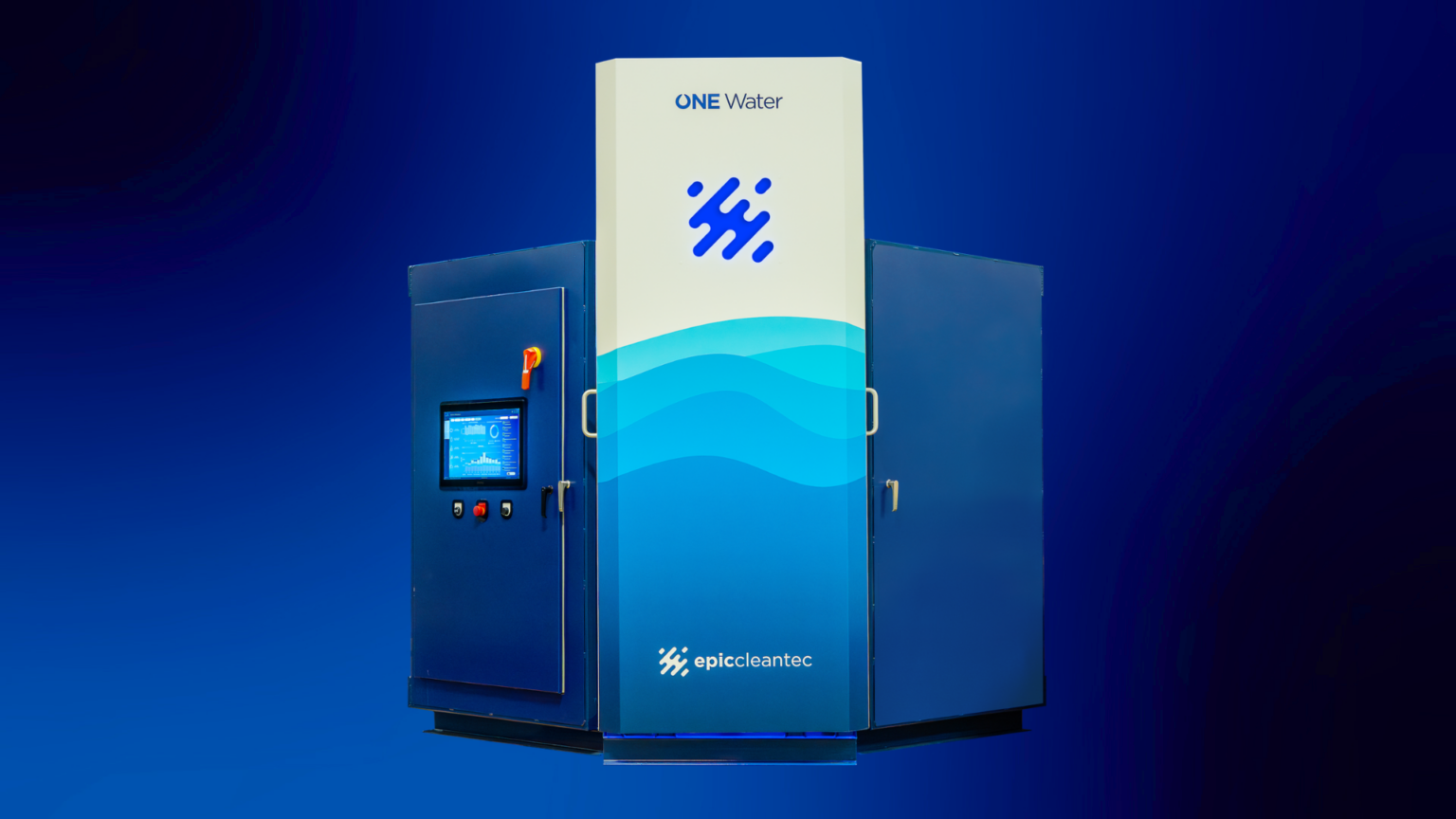
Architects and engineers must consider several unique constraints when selecting technologies for onsite water reuse systems. While many municipal treatment systems utilize open-air ponds for treatment, building scale systems must prioritize designs that adhere to space restraints and eliminate odor to avoid any impact to the building occupants. Membrane bioreactor (MBR) technology is an optimal system for the built environment due to the pairing of robust biological treatment with ultrafiltration membranes that maximizes removal efficiency, saves on system footprint, and streamlines operations & maintenance requirements. Epic Cleantec uses an MBR-based treatment train for most building wastewater projects, with customization to each project’s requirements and local regulations.
How the MBR treatment process works
The MBR-based treatment system process starts when untreated greywater or blackwater enters the system via an equalization tank, which serves as a buffer for flow fluctuations to maintain constant supply to the system. The water is then pumped to an aerobic biological tank, where most of the treatment happens. Dissolved oxygen is added to the biology tanks and the microbiology reduces the biochemical oxygen demand (BOD) and nutrients like phosphorus and nitrogen.
After 6-8 hours of retention in the biology tanks, the wastewater is then pumped through the ultrafiltration membranes. These UF membranes act as a physical barrier, separating solids and microorganisms from the treated water. The membranes produce filtered water that is then dosed with ultraviolet disinfection (UV) as well as chlorine disinfection to kill any pathogenic organisms that are present in the treated effluent. The MBR process (which is the sum of the biological treatment and the ultrafiltration membranes) coupled with UV and chlorine meet the log reduction requirements for safe discharge for non-potable reuse, though the dosage requirements may vary by jurisdiction and end use.
The Epic Cleantec OneWaterTM system uses best-in-class ultrafiltration membrane technology with a 0.04 µm pore size to maximize treatment and capture of particulates and pathogens. A micron (µm), or micrometer, is defined as one-millionth of a meter, or a little more than one twenty-five thousandth of an inch. For comparison, a single human hair ranges in diameter from 17 to 181 µm.
The difference between MBR, MBBR, and SBR technology
Other common systems used in small-scale operations, such as building scale or small district scale, are MBBR and SBR technology. Each technology has advantages and disadvantages that must be considered when choosing a system for a project.
Membrane bioreactors (MBR) offer excellent treatment efficiency, producing clean effluent with low levels of contaminants. These systems combine conventional activated sludge treatment with a high-quality membrane filtration system that utilizes bacteria and other microorganisms to break down organic waste. With MBR technology, operators can easily adjust parameters and optimize system performance based on changing conditions, allowing for more precision over the treatment process. The entire treatment process for a MBR system can take less than 10 hours. MBR systems have compact footprints, can adjust to varying influent conditions, and have the dual benefit of reducing organics concentrations while providing pathogen reduction credit towards regulatory requirements.
Moving Bed Biofilm Reactors (MBBR) use a biofilm process where microorganisms grow on small plastic carriers that move freely within the reactor. These carriers provide a large surface area for biofilm growth and help in the biological treatment of wastewater and can react to a high variability in influent water quality. MBBR systems can be a cost-effective option from a capital investment, and they also reduce some operations and maintenance requirements such as backwashing membranes that are required with MBRs.
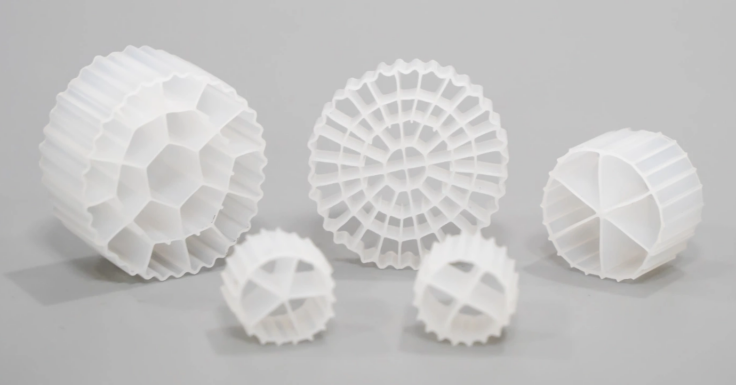
Example of different types of MBBR media plastic
Sequencing Batch Reactors (SBR) are recurrent biological treatment systems where wastewater is treated in batches through a series of steps including filling, aeration, settling, and decanting all within a single tank, utilizing gravity to help with separation during each phase. Because the SBR process happens within one tank, space is a concern as the entire daily wastewater supply will have to fit in one tank. In MBR and MBBR processes, the layouts can be more flexible as treatment steps are separated into multiple tanks and skids.
At a high level, MBRs rely on membrane filtration, MBBRs utilize a biofilm process, and SBRs operate in batch cycles. Each technology has its strengths and is suitable for different wastewater treatment applications based on factors like effluent quality requirements, space availability, maintenance costs, and operational flexibility.
MBR technology is typically the ideal option of choice for water reuse applications due to several reasons, as summarized above. In general, the consistent high effluent quality is key to meeting onsite reuse regulatory requirements. In multiple jurisdictions, including San Francisco and Austin, an MBR-based system is the basis of design for greywater and blackwater onsite reuse, though other systems may be selected to meet the log reduction targets.