14 lessons learned from designing, permitting, and maintaining onsite water reuse systems

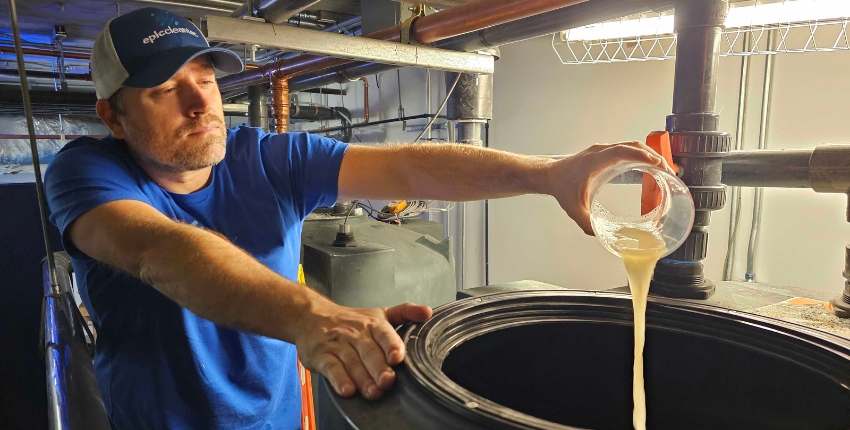
What you need to know for a successful implementation and long-term operation of an onsite wastewater reuse solution
Every project has specific needs, regulatory requirements, and its own purpose for adding an onsite wastewater reuse system. Whatever the reasoning, there is no one-size-fits-all solution; each system design needs to be custom to the project, which can present a unique set of challenges for architects and engineers unfamiliar with this technology or the implementation process.
Through our decades of experience designing, permitting, providing and maintaining these systems, we’ve taken note of some of the most common issues that arise. From room layout considerations to permitting process hurdles and ongoing maintenance training, we’ve outlined 14 lessons learned for a successful onsite wastewater reuse system.
Treatment System Design
- Design systems based on actual per capita usage or higher
Relying on an overly optimistic water balance will result in a system design that is not compatible with the building’s true water needs. With more of the population working from home, more water use occurs throughout the day, meaning tank and system sizing need to be adjusted. Additionally, many of the onsite water reuse calculators available online rely on lower demand values which are based on green building certification programs like LEED. While these calculators offer an aspirational view, using them to size a system can leave significant savings on the table. Sizing a system based on appropriate demand values, owners will see less municipal supply needed, saving more on water and sewer fees. - Integrate the potable makeup water flow meter with system controls
For systems reporting potable makeup water use to regulatory agencies for compliance purposes, it’s critical that the potable makeup meter measures potable flows in tandem with whichever flow control system is used. It also needs to be accurate at the full range of expected high/low flows. Having a flow meter that does not report to the HMI or that requires a manual reading is less efficient and opens the door to errors or gaps in reporting. Additionally, flow meters that cannot record lower flows are likely to report incorrect values as a result. - Consider ventilation and odor control methods ahead of time
Odor control mitigation considerations largely happen during the design phase and can be addressed with activated charcoal (carbon) filters; it’s much harder to correct this issue post-design. Ensuring proper ventilation in the treatment room is also a key factor in keeping odors at bay. Making sure these small but significant features are included in design results in a better end use experience.Treatment Room Design
- Room layout should include safety measures and sufficient drainage
It’s inevitable that there will be liquids on the floor at some point in an onsite reuse treatment room. As such, the flooring should always slope toward drains and there should be a sufficient amount of drains to minimize any pooling in the event of a spill. These systems typically require chemical treatment so it’s also important to plan for safety equipment in the system room like eye wash stations, chemical showers, spill kits, chemical hazard labeling, and a utility sink for operator use. - Incorporate allowance for future electrical needs
Designing the room with future electrical allowance is an often overlooked aspect of treatment room design. Modifications, additional hardware, or powered cleaning tools are sometimes needed, and without proper electrical allowances it can be much more costly to implement changes after the initial design. - Internet connectivity is a must
Remote access and control of onsite systems helps alleviate the need for frequent onsite operational visits, thus lowering the cost to maintain a system. Wi-Fi is typically unreliable in these rooms, as they are often in a building’s basement and surrounded by concrete. Running a dedicated hard line during construction gives operations and maintenance teams the connectivity needed to remotely view and manage system performance 24/7, increasing system reliability and saving operational costs. - Elbow space and head room are appreciated
It’s important to remember that systems are cared for by a person and they need to be able to easily access all angles of the system for regular maintenance, repairs, or retrofits. Room height also matters for tank access or membrane replacement; consider how overhead restrictions like fire suppression systems, ducting, and piping may affect system and tank access. Other equipment may be brought in to help lift heavy components like pumps or replacement membranes, so designing rooms with sufficient clearance and minimal ground level piping is ideal. - Don’t forget about storage space
Dedicated onsite storage is an often overlooked feature of the room design. Replacement parts, consumables, chemicals, cleaning equipment, etc. need to be accessible to the teams overseeing the system. Creating a devoted space for these items helps keep the room clean and accessible for operators and visitors alike.Permitting
- Timing is key for permit submission and grant funding
Every region has different processes and timelines for the permitting process. It can take anywhere from 6-18 months for permitting approvals, and grants or incentives will often impact submission and construction timelines. Permit submission involves coordination with various stakeholders, including local government authorities, building departments, and other regulatory bodies. Working with an experienced onsite reuse system vendor team can ensure optimal timing for submission and can help navigate complex regulatory landscapes. - Know the code
Plumbing codes and treatment requirements vary from city to city, so what works for one project or in one jurisdiction may not work elsewhere. It’s critical to understand which milestones can hold building permit issuance and that minor code differences can create major obstacles.Operations and Maintenance
- Onsite time and testing requirements vary
Incomplete or insufficient functional testing at startup can result in issues down the line. Ensure both the design engineer and long-term treatment system manager participate in functional testing. Certain treatment system types, especially with biological processes (like MBR), may take a while to establish the stable population of microorganisms needed to meet treatment standards and complete functional testing. Build in sufficient time for functional testing in the startup plan. - Simple adjustments can make a big difference
In rainwater and stormwater systems, dry seasons can cause standing water that can serve as mosquito breeding grounds. Using abatement solutions is a simple way to eradicate this issue. - Posted signage and purple pipes are required
Treatment rooms and all applications will need to have signage posted letting users know that reclaimed water is in use. Additionally, purple pipes (Pantone color No. 512, 522C, or equivalent) are a requirement for all alternative water sources. Specific requirements may vary by jurisdiction. - Make a plan
Operating and maintaining your onsite reuse system is a broader effort than you might think! Develop an O&M staffing plan that includes training building staff on the day-to-day maintenance to cut down on external operator expenses and ensure building staff know how to safely monitor the system. In the event of an emergency, system shutdown planning is crucial. Ensure there is always someone onsite that knows the shutdown procedure to avoid system damage or other issues.
Main Takeaway
Bring in water reuse experts early!
Incorporating water reuse systems into building design is a proactive approach to benefit both the environment and the bottom line, while also supporting the broader goal of sustainable development. Projects benefit most when an experienced team is brought in early to discuss all the necessary considerations for the wastewater reuse system and operations. Partnering with experienced professionals like Epic Cleantec ensures your project is thoughtfully designed, adheres to local and state regulations, and operates smoothly into the future.